6-6 機械設備・作業などの具体的な改善方法
(1)機械設備などの安全化の基本
リスクアセスメントに基づきリスクを低減させるための措置を検討する際は、機械設備の本質安全化を第一に考えることが重要です。
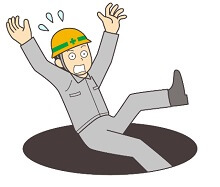
人間は注意力に欠けやすく、ミスを起こしやすい動物であるため、危険な作業を作業者が注意して行うだけでは安全は確保されません。このような人間の特性を念頭において、人間がミスを起こしても安全が確保できるように、設備や機械・工具などの安全化を図ることが重要です。
なお、機械設備の「本質安全化」とは、以下のようなものを言います。
・作業者がミスをしても人に危害を及ぼすことのないようにすること
・機械が故障しても、人の安全が保たれる機能を実現すること
建設現場においては、元方事業者は工事の施工に際して、事故や労働災害などの防止のために予想される危険性又は有害性を評価して、設計又は計画の段階で工法や使用する機械設備などを検討し、本質安全化に努めています。
しかし、本質安全化の観点から検討され設置された機械設備であったとしても、長期的使用による機能低下や、多業種による使用によって生じる危険性または有害性により、災害が発生するおそれがあります。
従って、工事中に発生する機械設備などの危険性または有害性を毎日の安全ミーティング、危険予知活動などから作業開始前に特定し、可能な対策を講じて労働災害などを防止することも職長の大切な職務です。
また、事故・労働災害の防止や施工の効率化、仕事のやりやすさなどを検討し、従来から使用してきた機械設備などを、可能な限りより良いものに改善していくことも望まれます。
(2)機械設備などの本質安全化の方法
機械設備などの本質安全化は、次のような事項を検討し実施します。
① 設計・購入時に行う本質安全化
- イ. 二重以上の安全対策が取られているようにする。
- ロ. 危険源と身体(の一部)が接触しない構造とする。
- ハ. 誤操作、間違いがないようなシステムとする。
- ニ. 機械の破損などを最小限にする構造や強度とする。
- ホ. 点検、修理など、保守が容易に行えるようにする。
- へ. 機械の使用中は作業者が危険区域に入れないようにする。
- ト. 作業者が触れる恐れのある箇所に鋭利な端部などがないようにする。
② 安全装置による安全化
- イ. 過巻防止装置
- ロ. モーメントリミッター
- ハ. トリップ機構
- ニ. ロック機構
- ホ. 安全ブロック、安全プラグ、レバーブロック
- へ. ヒューズの使用
- ト. 機械設備に異常、故障などが起きた時に安全側に働く構造
(安全を検出して機械設備に運転許可信号を出力する方式)
③ 危険部位の防護対策
- イ. 囲い・防護覆いを設置する。
- ロ. 安全距離を確保する。
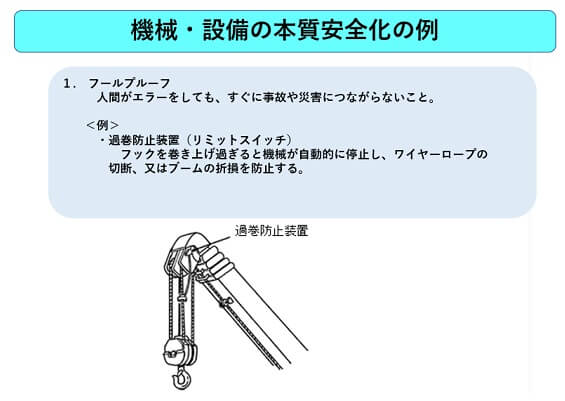
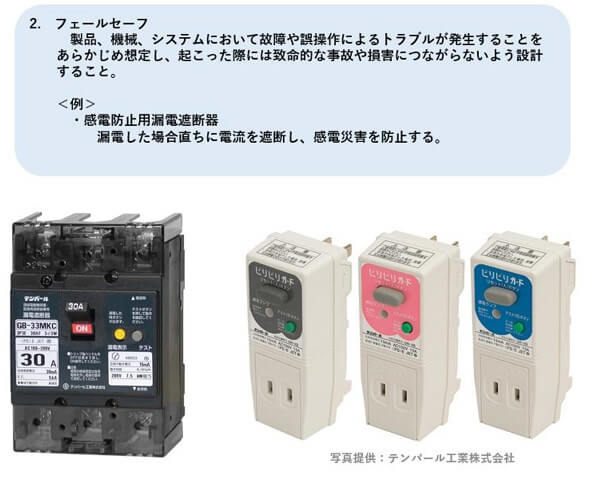
(3)作業方法の改善
製造業などでの作業(業務)改善は品質(Q)・原価(C)・納期(D)を対象としたものが一般的であり、中でも良く知られる手法として3ム(ムダ・ムリ・ムラ)に注目したものがあります。
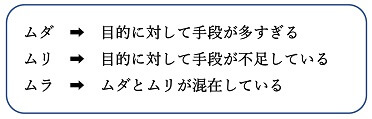
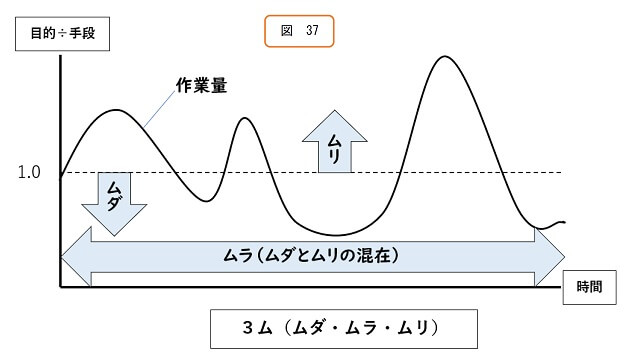
また、3ムは安全(S)にも大きく関係しています。ざっと考えても「ムリ」は失敗の元となるでしょうし、逆に暇な状態が安全なわけではありません。
例えば下の表は意識レベルについての研究結果ですが、手待ちなどで暇すぎると「Ⅰ」の「意識ボケ」状態に陥り、注意の作用は「不注意」、疲労や眠気を感じたり作業の信頼性は相当低下していることが考えられます。
・停電作業をしていて相方の作業が終わるまで手待ちが長く、「おーいスイッチを入れてくれ」と言われつい間違って隣のスイッチを入れてしまった
・荷降ろしまで時間があり運転席でボーとしていて声を掛けられ、慌ててエンジンを掛けたら急に動いてしまった
というような、普通の状態なら考えられないような失敗を起こしてしまうこともある危険な状態ということです。
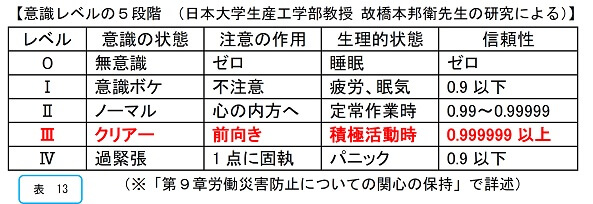
作業グループによる作業の具体的な改善について(例)
①対象となる作業の特定
まず、職長がリーダーとなって、改善しようとする作業を決めます。
・災害の発生した作業
・ヒヤリハットが発生した作業
・品質・原価・納期に問題の発生した作業
・その他3ムに関し特に問題があると思われる作業
②問題点の洗い出し
作業の手順3ムのそれぞれについて、作業手順書なども参考に以下の項目等に注目して問題点を挙げます。
ムダ(効率の悪い作業や付加価値をもたらさない作業)
技能のバラツキ
材料のバラツキ
設備のバラツキ
手順のバラツキ
仕事量のバラツキ
ムリ(疲労やケガの原因となる作業)
早過ぎる
重過ぎる
難し過ぎる
遠過ぎる
多過ぎる
高過ぎる
深過ぎる
熱過ぎる
ムラ(ムダとムリが混在している状態の作業)
作業や出来高のバラツキ
作業待ちの出現
能力と作業のバラツキ
③問題点の分類
問題点を「安全」「品質」「原価」「納期」「その他」に分類します。
④改善策の検討
問題点について「業務改善の4原則」などを参考に、改善策を検討します。
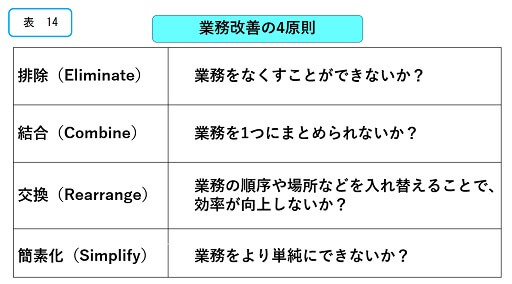
⑤改善策の決定・実行
改善策は「案」としてまとめ、管理者の承認を得たうえで実行・実践します。なお、必要があれば作業手順書を修正します。
⑥改善策の確認・定着
実践した改善策の効果を検証します。
また、改善策を実施したことによって新たな問題が発生することも考えられますので、作業者の評価・意見を聞くとともに、ある程度の期間は見極める必要があります。
地域・講習・人数に合わせてすぐに予約可能
講習会を予約する受講者様のご希望に合わせ、以下のタイプの講習会もご用意しています




このページをシェアする
講習会をお探しですか?